What are the production process steps of LED?
发布时间:2022-02-08 11:31
来源:萤光创新
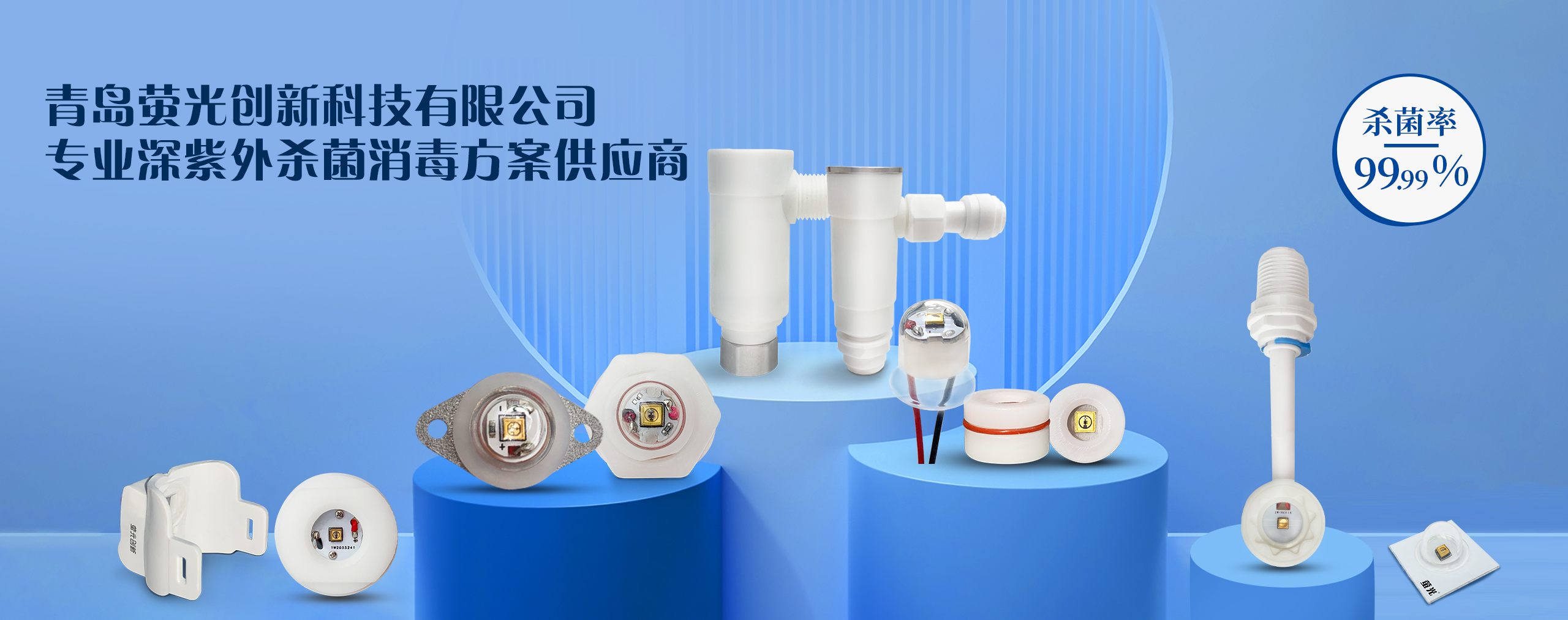
workmanship
a) Cleaning: use ultrasonic to clean PCB or LED bracket and dry it.
b) Rack mounting: prepare silver glue on the bottom electrode of LED die (large wafer) for expansion, place the expanded die (large wafer) on the spinel table, install the die on the corresponding pad of PCB or LED support one by one with a spinel pen under the microscope, and then sinter to solidify the silver glue.
c) Pressure welding: connect the electrode to the LED tube core with aluminum wire or gold wire welder to be used as the lead for current injection. Aluminum wire welding machine is generally used for led directly installed on PCB.
d) Packaging: through dispensing, the LED tube core and welding wire are protected with epoxy. Dispensing glue on PCB board has strict requirements on the shape of the solidified gel, which is directly related to the brightness of the finished backlight.
e) Welding: if the backlight is smd-led or other encapsulated led, the LED needs to be welded to the PCB before the assembly process.
f) Film cutting: die cut various diffusion films and reflective films required by backlight with punch.
g) Assembly: according to the drawing requirements, manually install various materials of the backlight in the correct position.
h) Test: check whether the photoelectric parameters and light output uniformity of the backlight are good.
LED packaging task
It is to connect the external lead to the electrode of the LED chip, protect the LED chip and improve the light extraction efficiency. The key processes include rack mounting, pressure welding and packaging.
LED packaging form
LED packaging forms can be said to be diverse, mainly according to different applications, the corresponding overall dimensions, heat dissipation countermeasures and light output effect are adopted. LEDs are classified into lamp LED, top led, side LED, SMD LED, high power LED, etc.
LED packaging process flow
1. Chip inspection
Microscopic inspection: whether there is mechanical damage on the material surface, whether the chip size and electrode size of lockhill meet the process requirements, and whether the electrode pattern is complete.
2. Expansion
As the LED chips are still closely arranged after dicing, the spacing is very small (about 0.1mm), which is not conducive to the operation of the subsequent process. We use a film expander to expand the film of the bonding chip, which is to stretch the spacing of the LED chip to about 0.6mm. Manual expansion can also be adopted, but it is easy to cause bad problems such as chip falling and waste.
3. Dispensing
Apply silver glue or insulating glue at the corresponding position of the LED support. The process difficulty lies in the control of dispensing amount. There are detailed process requirements for colloid height and dispensing position. Due to the strict requirements for the storage and use of silver glue and insulating glue, the waking, mixing and use time of silver glue are matters that must be paid attention to in the process.
4. Glue preparation
In contrast to dispensing, the glue preparation machine is used to apply silver glue to the electrode on the back of the LED, and then install the LED with silver glue on the back on the LED support. The efficiency of glue preparation is much higher than that of dispensing, but not all products are suitable for glue preparation process.
5. Manual prick
Place the expanded LED chips (with or without glue) on the fixture of the stabbing table, put the LED support under the fixture, and stab the LED chips to the corresponding positions one by one with a needle under the microscope. Compared with automatic rack mounting, manual stabbing has one advantage, which is convenient to replace different chips at any time. It is suitable for products that need to install a variety of chips.
6. Automatic rack mounting
In fact, automatic rack mounting is a combination of two steps: dipping (dispensing) and installing the chip. First, point silver glue (insulating glue) on the LED support, then use the vacuum nozzle to suck the LED chip up to the moving position, and then place it on the corresponding support position. In the process of automatic rack mounting, it is mainly necessary to be familiar with the operation and programming of the equipment, and adjust the glue dipping and installation accuracy of the equipment at the same time. The rubber nozzle shall be selected on the surface of the chip to prevent damage to the surface of the chip due to the diffusion of current on the chip.
7. Sintering
The purpose of sintering is to solidify the silver glue. The sintering requires monitoring the temperature to prevent batch defects. The sintering temperature of silver glue is generally controlled at 150 ℃ for 2 hours. It can be adjusted to 170 ℃ for 1 hour according to the actual situation. Insulating glue is generally 150 ℃ for 1 hour. The silver glue sintering oven must be opened every 2 hours (or 1 hour) according to the process requirements, and the sintered products must not be opened at will. The sintering oven shall not be used for other purposes to prevent pollution.
8. Pressure welding
The purpose of pressure welding is to lead the electrode to the LED chip and complete the connection of internal and external leads of the product. The pressure welding process of LED includes gold wire ball welding and aluminum wire pressure welding. The right figure shows the process of aluminum wire pressure welding. First press the first point on the electrode of LED chip, then pull the aluminum wire above the corresponding support, press the second point, and then tear the aluminum wire. In the process of gold wire ball welding, burn a ball before pressing the first point, and the other processes are similar. Pressure welding is a key link in LED packaging technology. The main processes to be monitored are pressure welding gold wire (aluminum wire), arch wire shape, solder joint shape and tensile force. The in-depth study of pressure welding process involves many problems, such as gold (aluminum) wire material, ultrasonic power, pressure welding pressure, selection of cleaver (steel nozzle), movement track of cleaver (steel nozzle) and so on.
9. Dispensing packaging
LED packaging mainly includes dispensing, potting and molding. Basically, the difficulties of process control are bubbles, multiple material shortages and black spots. The design mainly focuses on the selection of materials and the selection of epoxy and support with good combination. Manual dispensing packaging requires a high level of operation. The main difficulty is to control the dispensing amount, because the epoxy will thicken during use.
Qingdao fluorescent Innovation Technology Co., Ltd. has a professional postdoctoral team, focusing on the research of ultraviolet sterilization application. After years of deep cultivation in the ultraviolet industry, the company has obtained a number of national invention and utility model patents. At present, a number of sterilization module products have been put into the market. For more details, please visit the company's website at www.qdyingguang.com Com contact the company for the official account of WeChat.
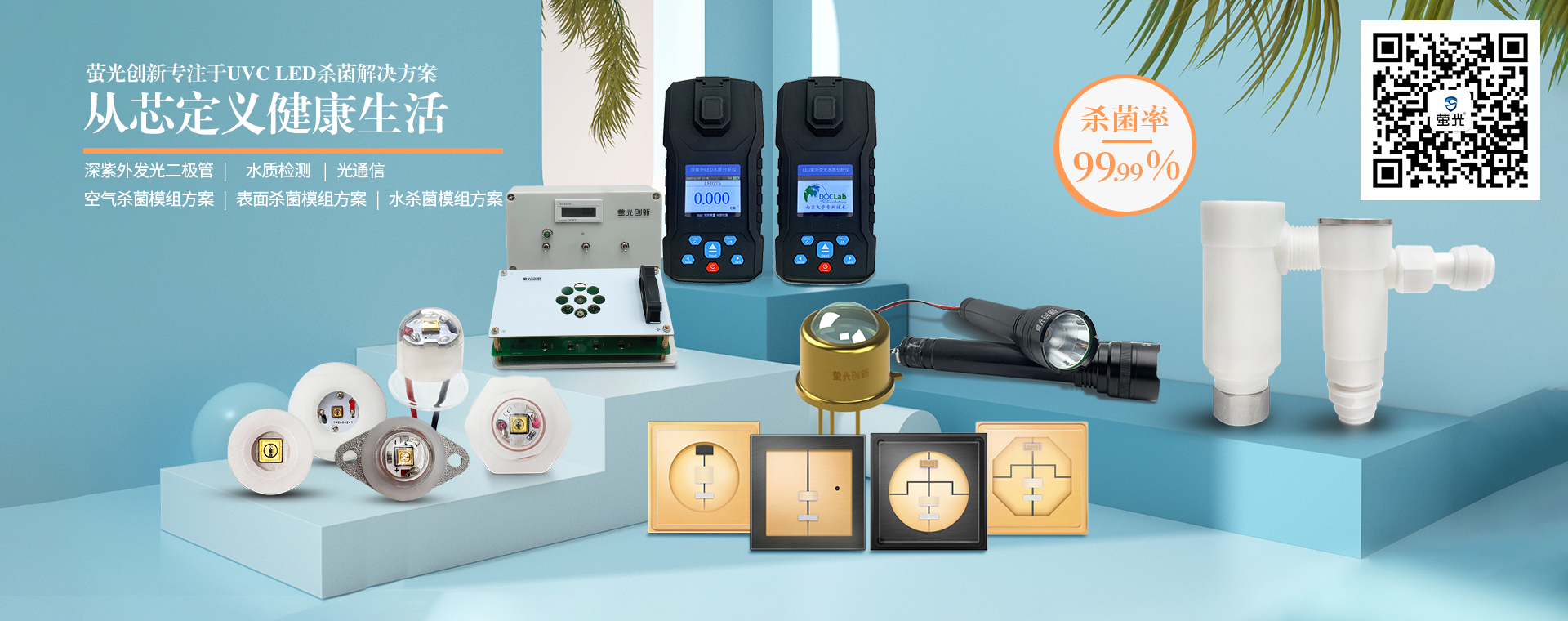
Keywords: 220nm, 230nm, 235nm, 240nm, 245nm, 250nm, 255nm, 260nm, 265nm, 270nm, 275nm, 280nm, 285nm, 290nm, 295nm, 300nm, 305nm, 310nm, 315nm, 320nm, 330nm, 340nm, 365nm, 395nm, 405nm, to39, uvworks, uvworks, UVC works, UVC eors, UV LED, UVA led, UVB led, UVC led, deep UV LED, UV sterilization Ultraviolet disinfection, ultraviolet sterilization, ultraviolet disinfection scheme, sterilization module, water purifier sterilization, terminal sterilization faucet, static water sterilization component, flowing water sterilization component, ultraviolet sterilization water purifier, sterilization faucet, toothbrush sterilization, water cup sterilization, surface sterilization, water sterilization, air sterilization and phototherapy